How 3D Printers are Changing Jewelry Making and Casting
Revolutionizing Jewelry Making: The Power of 3D Wax Printing
The 3D printing industry is experiencing explosive growth, projected to leap from $12 billion in 2020 to $35 billion by 2026. This remarkable surge is not only transforming large-scale manufacturing but also redefining the way jewelers and industrial professionals bring their ideas to life.
In dentistry alone, 3D printing is expected to hit $6.5 billion by 2025. This is thanks to the unparalleled precision of 3D printers achieving tolerances as tight as 0.1 mm and their ability to reduce production lead times by up to 75%. As a result, these printers have become a vital asset in modern production.
This guide takes a deep dive into wax 3D printing technology, focusing on how it supports detailed jewelry creation and industrial casting applications. Whether you're a jeweler or a manufacturer, mastering this tech can open doors to new levels of craftsmanship and efficiency.
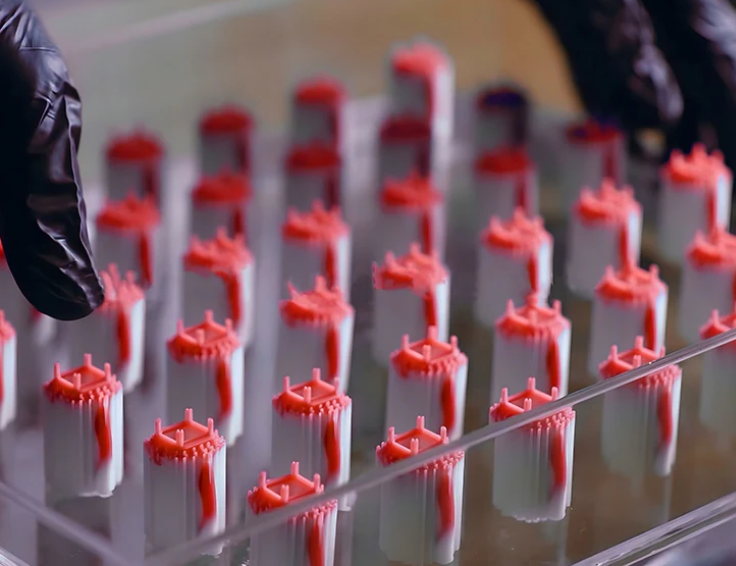
Understanding Wax 3D Printing Technology
Wax 3D printing is revolutionizing traditional manufacturing techniques. Unlike standard 3D printing with filament or resin which often creates final-use products, wax 3D printing is typically used as a step in lost-wax or investment casting. This bridges digital design and physical casting, allowing artisans to achieve detail that traditional methods can’t match.
The initial investment in these technologies is justified by long-term savings. Businesses reduce their need for tooling, minimize waste, and lower labor costs, making 3D wax printing essential in jewelry, dental, and industrial casting sectors. Choosing a wax 3D printer from a provider such as Romanoff International that offers live technical support can save time and frustration!
Setting Up Your Wax 3D Printer for Jewelry Making
Best Safety Practices:
-
Wear nitrile gloves and safety goggles.
-
Use a face mask to avoid inhaling fumes.
-
Maintain a workspace temperature of 68 to 72°F for optimal print results.
Model Prep Tips:
-
Export your design as an STL or OBJ file.
-
Tilt models at 10° on the X and Y axes to minimize supports.
-
Attach models to a wax sprue tree using a wax pen. Ideally, design sprues in the CAD file to reduce handling.
From Digital Design to Physical Casting
The journey from concept to creation begins with the right CAD modeling or 3D scanning. Programs like 3Design and Rhino provide specialized tools that mirror a traditional jeweler’s workflow, making it intuitive even for classic goldsmiths.
These digital files are translated into tangible models by your wax 3D printer layer by layer with resolutions as fine as 8 µm.
Support structures are added during printing and manually removed post-production. Here's how to prepare your printed models:
-
Clean using isopropyl alcohol or specialized solutions.
-
Remove supports using fine flush cutters.
-
Smooth any irregularities with fine-grit sandpaper.
-
Perform a detailed quality inspection.
Once cleaned, the model is attached to a casting tree and placed into a metal flask and surrounded by investment plaster. Once solidified, the now hardened flask is placed into burnout oven to remove the wax or resin leaving behind a negative cavity of your model.
After the wax or resin burns out, molten metal can then be poured in via a castin, creating a perfect metal replica. Once cooled, it’s separated, polished, and finished to perfection.
The future of jewelry making and casting is being shaped by innovation. At Romanoff International, we’re proud to be part of that transformation. With precision-driven machines like the Tiger3D Printers and the reliable, user-friendly FlashForge 3D Printers, creators at every level can now bring their most intricate designs to life with unmatched speed, detail, and efficiency.
Whether you're crafting custom engagement rings or managing production-level casting operations, our printers simplify workflows, cut lead times, and deliver professional results.
From digital design to physical casting, Romanoff’s state-of-the-art 3D printers empower jewelers and manufacturers to scale smarter, work faster, and create without limits.
Ready to make your next masterpiece? Explore our full range of 3D printers here and discover what’s possible when precision meets passion.
Comments
Leave A Reply
Your email address will not be published.